The purpose of doctor blades for flexo printing
Scraping action to meter ink by flexo doctor blades was adopted from the rotogravure print process. In fact, flexo made its the biggest print quality gains by moving to higher line anilox and eliminating the surface ink film. The excess ink requires as well as more dry time and energy consumption, so as potentially adds undesirable print lines. In addition, the thicker ink film more rapidly overwhelms the plate’s raised image resulting in dot gain, dirty print and mid run press stops to clean the plate.
Flexo doctor blades are manufactured from a variety of materials, each offering particular advantages and suited for special printing applications.
Materials we use to make doctor blades for flexo printing
We use only well known and checked steel providers for supplying steels for our manufacturing processes. This high quality and reliable delivery raw steels enable us to manufacture your blades precisely for each application and deliver them always on time.
We manufacture doctor blades from
- carbon steels
- micro-alloyed tool steels
- stainless
Additionally, to improve blade lifespan, hardness and maximise corrosion resistance, we offer premium quality blades with chromium and tungsten alloys.
Please read about our Doctor Blades Types.
What tip is the most popular for flexo doctor blade?
A doctor blade with a radius edged tip, as it is well accepted, is the mostly used in flexographic print. Safety operation, longer run time and price efficiency are the main factors that determined this preference.
The next choice is the beveled edge, and the less common is lamella edged blade.
We supply all our Gravure Doctor Blades in all standard edge profiles:
- Lamella edge
- Bevel edge
- Round edge
At what angle is doctor blade flexo printing to the anilox?
In the flexo process, the challenge is to set a blade to the anilox at roughly 30 degrees to 35 degrees and keep it there. Therefore, most of doctor blade metering systems are preset to position the blade at the optimum contact angle.
What size should be flexo doctor blades?
The contact area of the blade stays a significant factor in controlling the amount of ink. To lower hydraulic impact, it has been accepted that the width of the contact should be as narrow as possible. The higher hydraulic presser, during run processes, lifts the blade and allows more ink to pass through. Therefore, to reduce negative impacts, a thicker blade is often preferred.
Making the correct choice isn’t always obvious, as sometimes a thicker blade provides a thinner contact area. If you are not confident what size doctor blade you require for your printing, please contact us and our technical experts would discuss your requirements.
If you require an urgent quote please contact us on +44 (0) 114 244 0527 Option 2
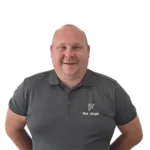
Please contact Nick
to discuss your Doctor Blades
Office: +44 (0) 114 244 0527 Ext: 129
Email: nick.wright@fernite.co.uk
Mobile: 07480 254837
WhatsApp: 07480 254837
Mon – Thu: 8.30am-5.00pm
Fri: 8.30am – 3.45pm
Sat-Sun: Closed
If you prefer to send a contact form
please follow the link
If you require an urgent quote please contact us on +44 (0) 114 244 0527.